RHI MAGNESITA INDIA LTD.
February 15, 2022 | Stock Talk, Deep Dives
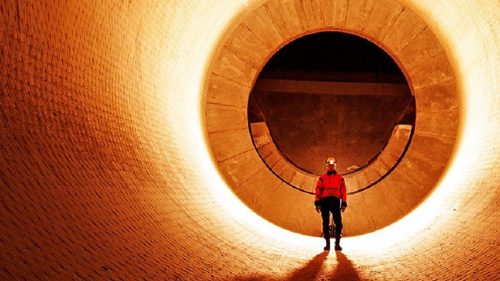
Indian Refractory Industry
Inside the report
- What led us to research this industry?
- Understanding the Product: Refractories
- Understanding the Refractory Industry in detail
- Explaining, why this industry can do well, going forward
- RHI Magnesita India Ltd.
Research Analyst - Gunjan Kabra (info@gunjankabra.com)

What led us to research this industry?
We did a top-down analysis at macro level and analyzed that Indian capex cycle can rebound. India’s capex cycle has been muted since last 10 years as private capex was flat. It was only the government capex that had supported infrastructure spending with 13% CAGR over FY10-20. What has changed now?
- Investment cycle has bottomed out. Investment contribution to GDP has reduced to 26.7% in FY21 from peak of 36% in FY07.
- Healthy Balance Sheet and Good Cash Flows of corporates
- Accommodative Monetary Policy: Low cost of funds & Adequate Liquidity
- High Demand from domestic as well as export markets
- Cut in corporate tax rate for new capex (15%)
- Reforms done in the past like RERA, GST etc.
- Government initiatives to boost manufacturing activities like PLI Scheme, import substitution initiatives
- National Infrastructure Pipeline of Rs. 1.1 trillion over FY20-25 which is twice of the total spending done in FY13-19.
- China plus one strategy helping India to boost manufacturing activities
- Indian Renewable/Clean Energy in focus
Government spending is the first to revive in any capex cycle. This gives confidence to private players to make expansion. Hence, we see an upsurge in capital expenditure. Order Flows for capital goods companies are growing.
For instance, Thermax Limited is engaged in the business of manufacture and sale of boilers, heating and cooling equipment, industrial chemicals, and water and waste management equipment. The following table highlights the order book trend.

JSW Steel, for instance, plans to spend around ₹28,000 crore to expand steel-making capacity from 24.5 million tonnes (MT) to 36.5 MT by March 2024,
Tata Motors is investing ₹28,900 crore in subsidiary Jaguar Land Rover and hydrogen fuel cell vehicles in FY2022.
PLI Scheme will be a key driver of Private Sector Investments

With rise in these infrastructure/construction activities, capacity utilisation of steel will increase. The share of building and infrastructure construction in overall steel consumption is 60-65%.
Staying true to our investment style, we have chosen a company whose product is irreplaceable, plays a pivotal role in the capex cycle, indirect play on the steel sector. This sector is less volatile when compared to steel with limited downside. The sector is Refractory Industry.
Understanding the Product: Refractories
- What are Refractories?

- Refractories are ceramic materials designed to withstand very high temperatures (exceeding 1,200°C) without undergoing physical or chemical changes while remaining in contact with molten slag, metal and gases.
- In simple words, Refractories are used for lining furnaces, kilns, reactors, and other vessels which hold and transport hot mediums such as metal and slag.
- How it helps?
- Serves as a thermal barrier between the hot medium and the wall of containing vessel
- Withstanding physical stresses(force) and preventing erosion of vessels
- Providing thermal insulation
- Protecting against corrosion
- Improvement in production and performance
- How important are refractories? Refractories are essential protectants for all heat-intensive production processes, including iron and steelmaking, cement production, glass, ceramics, aluminum, and nonferrous metals, paper and pulp, petrochemical processing, power production, and waste incineration. Without refractories, these industries and the products they produce would not exist.
- Characterized as Consumable or Investment Goods: depends on the end user industry
- Consumable Goods (75% of the total demand- Steel Industry)
- Full Line Contracts which includes systems and solutions for complete refractory management
- Demand is correlated to output
- Mainly caters to Iron and Steel Industry
- Investment Goods (25% of the total demand- Other Industries)
- Longer Investment Cycles
- Customized solutions based on the specific requirements of various industrial production processes
- Project driven demand cycles
- Consumable Goods (75% of the total demand- Steel Industry)
This point is explained in detail in the next points.
- Critical product, yet represents 3% of COGS in steel manufacturing and less than 1 % in other applications. Why critical? Any failure in the refractories results in a great loss of production time and equipment. The type of refractories used also influences energy consumption and product quality. Hence, the issue of getting refractories best suited to each application is of highest importance. Economics greatly influences these issues. The refractory best suited for an application is best is not necessarily the one that lasts the longest, but rather the one which provides the best balance between initial installed cost and service performance.
- An essential product in capex driven economic activity: Where is it used? 75% of the refractory demand comes from Iron and Steel industry and the remaining is from cement, glass, non ferrous and energy/environment /Chemicals.



2. Types of Refractories

Functional/Special Refractories
- Competition is comparatively less in this segment
- Other segments are quite competitive
This classification of refractories will help you to understand where is it used in the steel industry and also the margins vary of each product profile. This will also enable you to differentiate the product mix of refractory companies.
The focus is on iron and steel industry because the major demand and recurring demand comes from this sector.
3. Where is it used in steel industry?

In order to understand where refractories are used, it is important to understand the manufacturing process of steel. Here, I’ll be discussing the process in a broad sense to understand, how and where refractories are used while making steel.
Globally, steel products have been mainly manufactured via primary steelmaking process that constitutes two major routes. These are:
- Blast Oxygen Furnace (BOF)- Primary Steel Making
- Electric Arc Furnace (EAF)- Secondary Steel Making
Blast Oxygen Furnace (BOF)
It is a large integrated steel making facility where primary steel is produced. It is useful in making bulk quantity and good quality. These plants are large in capacity ranging from 1to 5 million tonnes per year are spread in large areas. They can take advantage of economies of scale.
Major Raw Materials: Iron Ore (80-90%), Coking Coal
Other Materials: Limestone, Scrap Steel (10-20%)

- How steel is made in this method?
- The coke along with iron ore and limestone is heated in Blast Furnace to form pig iron.
- The molten iron along with steel scrap is added to the Blast Oxygen Furnace where it is further refined. Oxygen is blown onto the molten iron and converting into molten steel.
- Steel ladle is used to transport liquid steel from BOF/EAF and also act as a reactor where refining of steel takes place to reduce impurities, carbon, alloy addition. Here, different alloys like Ferro Manganese and Silico manganese are added.
- After completion of secondary refining of steel in steel ladle, the liquid steel is transferred from steel ladle to tundish through the slide gate flow control system. Slide Gate valve is used in tundish also to control the liquid flow from tundish to moulds. The ladle flow control system is consisting of the following items:
- Ladle nozzle
- Slide gate plates
- Collector nozzle
Electric Arc Furnace (EAF)
EAF have a much simpler input process.
Major Raw Materials:
- Scrap Steel
- Graphite Electrodes (a device to conduct electricity to melt scrap)
- Direct Reduced Iron (DRI)
EAF (Electric Arc Furnace) use electric arc with high power to generate the required heat to melt the steel scrap of recycled and transform into the desired composition of steel. The steel-making process on EAF is not dependent on the BF production since the actual input is scrap steel and certain quantity of pig iron and graphite electrodes.
The steel produced from the BOF and EAF is again refined to get the required chemical composition; these are secondary refining processes of steel making. Step iii. & iv. mentioned in the BOF section is same in both.

Refractory Application for Steel Ladle

The numbers in the picture refers to the numbers mentioned in the above types of refractories table.


4. Raw Materials Used
Principle raw materials used in the production of refractories are:
- Brown Fused/ White Fused Alumina (manufactured from Bauxite: Not the same alumina used in manufacturing aluminium)
- Magnesia
- Silicon Carbide
- Zirconia
Understanding the Refractory Industry in detail
- Industry Characteristics:
- Fragmented Industry

In last 6 years, IFGL Refractories have gained market share by 0.8%. While Vesuvius India and Tata Krosaki Refractories have lost market share by 3% and 5.3% The share of RHI Magnesita India remained same. 70% of the refractories consumed in India are locally produced and 30% are import dependent. Out of which 2/3rd is imported from China.
- High Entry Barrier Business
- Since, it is a critical raw material, relationship with buyer is very important
- Customer Stickiness
- Product Quality is very important as explained above
- Continuous R&D is required to be more efficient , only large players have this capability
- Raw Material security is very important
- Consumable Product, less volatile over long term Steel Production will happen irrespective of the steel cycle. The fixed cost of shutting down the plant during downcycle is quite high. Hence, the steel plants will continuously run and the demand for refractories would be stable. The profitability of the steel cycle varies depending on the cycle. This explains why refractory industry is less volatile and consistent.

- Consistent Growth seen in Refractory Business irrespective of steel cycle

Notes:
- The growth rate in RHI Magnesita India in 2020 and 2021 is not comparable as there was a merger
- The growth rate was negative in Vesuvius India in 2020 and 2021 as the company lost market share
Overall, we can say that refractory business is an indirect play on steel industry and capex cycle with less volatility.
2. Supply Side Dynamics: Understanding the Raw Material Industry
- Raw Material Security is challenging: Around 40% of the raw material is imported from China by refractory players in India. For RHI India it is around 20-25%. Raw material security has been a problem in the industry even before COVID. The pandemic has accelerated the trend of shortage of raw material. Generally, the rise in raw material prices can be passed to the companies as the % to COGS is quite low. This happens with a lag.
- Benefit of Vertical Integration: The companies who have integrated mines are the ones who are expected to perform well in the coming years. This can lead to consolidation in the otherwise fragmented industry. The graph below depicts the benefit of vertical integration in the refractory industry

- Recent Trends:
- Volatile Raw Material Prices: Prices of raw material has increased because of supply chain disruptions from China, high freight costs.
- Shift to other countries for procuring raw material: In one of the recent interviews, VP of Tata Krosaki stated that “We still depend on China for alumina and magnesia based refractory raw materials, But, we have slowly moved to other destinations.” Other destination includes Europe, Brazil, South Africa and Turkey, but the cost is 30-40% higher. The company with integrated mines will benefit as they have raw material security and margin expansion. For instance, RHI Magnesita India has mines in Brazil, Turkey and Europe which makes for 40% of the total raw material requirement for the India plant. Around 20-25% is imported from China and rest is sourced locally. For peer companies like IFGL, they don’t have their own mines and is dependent on China for their 40% of the material requirements. Vesuvius India also faced shortage of raw material.
- Recycling of raw materials leading to cost savings: Use of recycled refractory materials will lead to savings in raw material costs by almost 30%. Companies like RHI Magnesita India have upto 12% usage of recycled raw materials. The availability of the same is scarce and not all players will be able to scale up the usage. RHIM has acquired magnesia recycling facility in Cuttack. The company who provides complete business solutions will benefit more.
Explaining why this industry can do well, going forward
- Shortage of Raw Material can lead to consolidation in the industry: As mentioned, companies who have captive mines can survive and benefit on account of
- Raw Material Security: less import dependent and high localisation
- Superior Margins
2. The industry is moving towards full line contracts under Total Refractory Management (TRM) services or complete business solution model. Steel companies prefer this model. Here, the company provide a broad range of tailored services at customer sites such as refractory installation, recycling, digital and supply chain services. These drive process efficiencies, reduce costs and generate sustainable benefits, thereby creating value for customers as well as for the companies.
RHI Magnesita, the parent company is now providing this service in India too through RHI Magnesita India. Vesuvius India and TRL are other players who provide this service.

This is a big change and how will this benefit?
Refractories installation is technical. Attention to detail is crucial for a proper refractory installation. For instance, how much water needs to be mixed, temperature control while installation, adequate storage, drying out process. If the installation isn’t correct, the refractory lining will crack and weaken quickly resulting in risks to workers and refractory projects. Steel Companies would need a skilled refractory installation contractor for proper refractory installation.
Every refractory project is unique and needs customisation.
Model II: Dual benefits to Steel and Refractory companies:
- Refractory Companies- Scope to gain market share and easy availability of recycled material
- Steel Companies- can get customised refractory solutions as working with the refractory manufacturers directly. Right usage of refractory materials can improve production and efficiency.
Globally, refractory companies only provide complete installation to steel companies. RHI Magnesita India is trying to bring the same model to India. It would be easier for companies who has a complete basket of refractories to provide such services.
Why Refractory Maintenance Practice is important?
Refractory maintenance practice is important to maintain availability and extend campaign life. Materials for maintenance are very important as the volume of the maintenance materials consumed over a campaign may be up to two times the volume of original brick. Maintenance helps to balance the wear of refractory lining due to excessive wear in an area of repair whether the damage done mechanically or chemically

A typical cost curve is shown in the figure. The brick cost shows the cost of lining if the maintenance is not considered. Total cost is increasing from brick cost when the vessel is becoming old. There is a possible end of campaign in the absence of maintenance at a life of 4000 heats.
The life is extended to 12,000 heats by maintenance.
3. Steel Production is expected to remain high on account of:
- Revival in capex cycle leading to higher economic activities as explained in the beginning of the report.
- Strong export demand for steel and less import because of China plus one strategy and supply chain disruptions.
RHI Magnesita India Ltd.
- Why RHI Magnesita India ?
- Market Leader in Indian Refractory Market with ~15.9% market share
- Can be a direct beneficiary of the expected consolidation in the refractory industry (market leader)
- Total Refractory Services (TRM) can contribute significantly to revenues and margins as the company is moving towards this service. The benefit of this is highlighted above. This will also help the company to cater to large players.
- Superior Margins than peers and comparatively lower on cost curve on account of
- Well knit global supply chain network
- Vertical integration: Captive Mines leading to better raw material sourcing compared to peers. Hence, superior margins. We have seen this in the above section. Vesuvius India and IFGL are dependent on imports from China for their raw material requirement. RHI Magnesita India can source its raw material from parent company, RHI Magnesita. Further, localisation and recycling is leading to reduced demand from imports.
- R&D Facility: Established R&D in Bhiwadi in Nov 21. The aim is to develop 3 new products in the shaped refractory products.
- Better capacity utilisation than competitors: Industry Capacity Utilisation is around 50-60%. The company is operating at 85% capacity utilisation.
- Better Product Mix is also leading to higher margins: The company is into Tundish Management which is a niche area where it gets higher margin. Almost 15 percent of its business comes from managing the process flow control for the steel companies which again is a very high margin business.
- Slide Gate Refractories: Special Refractories Slide Gate Plate Refractories are installed on the ladle’s bottom for regulating the flow of liquid steel from Ladle to Tundish.
- Isostatic Refractory: a high margin business, also used in exports Refractory components for the protection of steel from oxidation reactions and other environmental contaminations in the transfer process from laddle to tundish and from tundish to continuous casting machine.
- Capacity Expansion Plan: The company has recently announced a capacity expansion plan of Rs.400 crores for the next 3 years. The focus of the parent company is on the Indian market. The company aims to make India as the manufacturing and R&D hub for its Asia and Africa market. According to management interviews, the company plans to increase around 25-30% of the total capacity every year. In one of the articles, it was also mentioned the company can make acquisitions too.
2. Installed Capacity and Planned Expansion
- Cuttack Plant: The company acquired a plant at Cuttack manufacturing Magnesia Bricks in 2019.
.The company plans to increase capacity by de-bottlenecking in phased manner from 10k tonnes to 18k tonnes. This is part of ORL. Benefit of this plant:- Magnesia Bricks are highly imported. Domestic demand is around 300k tonnes. 75% is imported from China. This will increase localisation helping in import substitution.
- Higher heat resistance than Alumina bricks
- Cost Savings due to recycling

- Bhiwadi Plant (Rajasthan): Manufactures High Margin Products like Slide Gate and ISO This is a part of Orient Refractories Ltd.

- Vizag Plant: RHI Clasil (Manufactures Basic Products- Alumina Bricks and Castables)
- It does Contract Manufacturing (Cost +10%) for RHI Entities
- Geography Wise Revenue: Exports: 60%, India: 40%
- Installed Capacity as on FY21 is 65000 tonnes Expansion: 25000 tonnes(Q3 FY23)
- Scope of Margin Expansion is less
- Caters to Steel and Cement Industry
- RHI India: It’s a trading company sourcing from various RHI entities.
3. About the Company
RHI Magnesita India Ltd. has been incorporated in 2021 with merger of three RHI entities
- Orient Refractories Ltd.
- RHI Clasil
- RHI India Pvt Ltd.
In 2013, ORL was acquired by RHI, Austria. Prior to this Rajgarhia family owned and managed the company. Post the acquisition, ORL was able to improve efficiency and quality and take advantage of the strong network globally. In 2021, the company got merged with other unlisted entities in India.

Geography Wise Revenues: India- 75% Exports- 25% The company plans to increase export share to around 30-35% in 2-3 years.
4. Key Risks
- Volatility in Raw Material Prices
- Downturn in Steel Industry
5. Management Quality
- The company should at least have 50% independent directors in the BOD Committee. RHI Magnesita India has 3 out of 7 as independent directors.
- The audit committee is chaired by Independent Director
- Remuneration as a % of PAT is optimal
6. Competitive Scenario
- Vesuvius India Ltd.
- Installed Capacity: 2,75,000 tonnes
- Raw Material: Import Dependent The company is operating at low- capacity utilisation The company has lost market share in last 5 years.
- Product Mix:


- IFGL Refractories Ltd.:
- IFGL Refractories Ltd. is a leading manufacturer of specialised flow control refractories.
- Installed Capacity: 27 lakh pieces of shaped refractories and 52k tonnes of Unshaped Refractories.
- Products Overview:
- Isostatic Refractories
- Slide Gate Refractories
- Tube Changer System & Refractories
- Nozzles
- Monolithics & Cast Products
- Raw Material: Import Dependent (40-45%)
- Market Share: 5.8% in 2015 to 6.6% in 2021
- Expansion plans:
- Odisha: Rs. 10 crores for normal capex by debottlenecking H1 FY23
- Kandla: Rs, 10 crores in HY22
- Vishakhapatnam: Project cost of Rs. 30 crores have been completed Q2 FY22 (48000 tonnes) Project cost of Rs. 20 crores is expected to be completed by Q2 FY23


Why RHI Magnesita India over IFGL?


- TRL Krosaki Refractories Ltd. (Unlisted Player)

The product mix is good, focus is on domestic market with a large market presence in stainless steel market. But the same is not reflected in EBITDA Margins and the company has been losing market share since 2015.
RHI Magnesita India has a strong presence in Special Refractories.

- Calderys India (Unlisted Player)
- Subsidiary of France based Imerys Group.
- The company is more into unshaped refractories
- Imports raw material from China
- 40-45% of the total revenue comes from iron and steel industry
- Revenue in 2020- Rs. 662 crores

- Dalmia Refractories Ltd. (Unlisted Player)
- Product Mix catering to cement and iron & steel industry
- Products: Bricks & Castables

RHI Magnesita India Ltd. - Financials
- Income Statement


RHI Clasil Ltd: Financials

RHI India Pvt. Ltd. : Financials

Outlook Interpretation –
Positive – Expected Return of 12%+ on annualized basis in the long term
Neutral – Expected return in the range of +/- 12%
Negative – Expected return in negative
Disclaimer: Niveshaay is a SEBI Registered (SEBI Registration No. INA000008552) Investment Advisory Firm. The research and reports express our opinions which we have based upon generally available public information, field research, inferences and deductions through are due diligence and analytical process. To the best our ability and belief, all information contained here is accurate and reliable, and has been obtained from public sources we believe to be accurate and reliable. We make no representation, express or implied, as to the accuracy, timeliness, or completeness of any such information or with regard to the results obtained from its use. This report does not represent an investment advice or a recommendation or a solicitation to buy any securities.
Niveshaay RHI Magnesita India Research Report
Disclaimers and Disclosures
SEBI Registration No. :INH000017338, IN/AIF3/24-25/1571, IN/AIF2/24-25/1607 | BASL Membership ID: 6276
Investment in Securities Market are subject to market risks. Read all related documents carefully before investing. The securities quoted are for illustration only and are not recommendatory. Registration granted by SEBI, membership of a SEBI recognized supervisory body (if any) and certification from NISM in no way guarantee performance of the intermediary or provide any assurance of returns to investors.