Indian MDF Industry
January 17, 2022 | Industry Insights
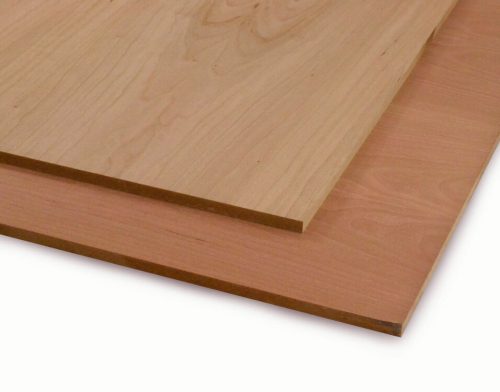

THIS REPORT COVERS
WHY MDF INDUSTRY? | INDIAN FURNITURE INDUSTRY |
ABOUT MEDIUM DENSITY FIBER BOARD (MDF) | MDF VS PLYWOOD |
EXISTING PRODUCTION CAPACITIES & PROPOSED CAPEX OF TOP ORGANIZED PLAYERS | CONCLUSION |
Research Analyst: Ramswaroop Agarwal (rsa0308@gmail.com) & Kartik Mediratta (Kartikmediratta64@gmail.com) |

- Growth opportunity size
The use of Medium Density Fibreboard (MDF) is increasingly finding market acceptance over plywood and India is no exception. Its global market size is estimated at 105.16 million CBM (USD 50.2 billion) in 2021. It is expected to witness a CAGR of 9.6% in the period of 2021-2026. In India, the MDF market size is estimated to be 2.8 million CBM (i.e., Rs. 3000 crores) in 2021. It is expected to grow at CAGR of 15-20% to Rs. 6000 crores by 2026.


- Shifting demand from plywood to MDF can foster market growth
The Indian Furniture Industry (especially the residential and home furnishing segments) continues to be dominated by plywood. Globally, the MDF to plywood consumption ratio is 80:20, but in India, the ratio is skewed in favour of the plywood at 20:80. This number suggests that there is enough room for the growth of MDF in the country in the future.

According to Industry experts, it is estimated that the MDF : Plywood ratio in India will improve to 50:50 by 2030. This presents a strong growth potential for the MDF industry in India. It is expected to gain market share of low & medium grade plywood (which constitute 85% of the plywood market in India)

- Cost advantage over plywood to end users
As both MDF and plywood have similar properties, both have been largely utilized in the manufacture of furniture such as tables, sofas, beds, and library shelves. MDF costs significantly lower than plywood while being devoid of particle grain and knots in its structure. Owing to these properties, this fiberboard proves to be an excellent alternative to plywood for application in areas wherein moisture and impact resistance are not the primary requirements.
Moreover, MDF has proved to be an excellent material for the formation of partitions in office spaces to ensure privacy and social distancing between the employees, which has been a key reason behind the sustenance of the material demand in the time of coronavirus. As many companies have taken up projects to renovate the offices to provide a homely feel to the returning employees after the reduction of lockdown restrictions, the industry is expected to stay healthy in the near future.
MDF’s market share is further expected to increase with the rising prices of Poplar Timber, a chief source of economy grade plywood in North India.
- MDF production in India
In India, MDF has penetrated all the regions in terms of market presence and is rapidly advancing in terms of both consumer demand as well as production capacity. The production capacity has grown by more than 12x from 0.15 million CBM in 2010 to 1.8-1.9 million CBM in 2021. Further, it is expected to witness a CAGR of 20-25% in the period 2021-2030.

- MDF industry is characterized by Strong Entry Barriers
- Capital intensive industry: High fixed & working capital investment
- Requirement of strong dealer network
- Licensing requirements for both greenfield & brownfield projects
- Higher gestation period: Companies installing MDF plant have to wait for 2-2.5 years for reaching optimum capacity
- Raw material procurement is what differentiates the efficiencies and performance of the companies
Due to this, it less likely to face competition from the unorganized segment, resulting in larger market share for the organized players and higher growth potential.
- Growth Drivers
- Growth in Real Estate Sector:
- Low cost of funds have increased investments in housing and other real estate investments
- Home affordability in India at decade best in 2021. For most part of last 5-6 years, residential prices corrected leading to better affordability, however, the recent reduction in home loan rate to below 6.5% has been a deciding factor in significant improvement in home affordability in the last 24 months. Also, Over the last decade housing market has undergone a structural transformation on both demand as well as supply side. This has made the environment for home buying relatively attractive and safe. This translate into higher demand for interior and furniture products.
- IKEAZIZATION of Furniture Industry: IKEA has emerged as the global leader in ready-made furniture industry. It has become the one-stop solution for new-age and cost-effective furniture. IKEA procures around 20% of its products from India which is expected to grow to 30% over next 2 years. This will drive growth in the Indian furniture and wood panel industry.
- Growth of Online Home Décor Platforms: Higher penetration of online home décor platforms such as Pepper Fry, Fab Furbish and Urban Ladder has contributed further to the demand of ready-to-assemble (RTA) furniture.
- Reduction in Furniture Cycle Time: As more and more people take to revamp their homes to adapt to their changing working styles, the demand for smart, sophisticated and comfortable furniture has seen an upward trend. Also, with higher disposable income, the span of home refurbishing cycle has gone down from 15 to 20 years a generation ago to 7-8 years.

- Demographics Factors
- Young Population India is home to a fifth of the world’s youth population: India’s youth is both Brand & Quality conscious coupled with cost-sensitiveness. This will drive demand for cost-effective branded furniture paving way for growth of the organized players of the Indian furniture industry who believe in providing highest grade of quality and customer satisfaction.
- Rapid pace of urbanisation: Rapid urbanization has also contributed to exponential growth in the real estate sector. It is estimated that there is a shortage of around 10 million housing units in urban India. According to industry research, supply of additional 25 Million units by 2030 is required to meet the growing urban demand.

The size of the Indian furniture market is estimated to be around USD 25-30 billion. It is expected to grow @ CAGR of 12% in 2021-26.
The Furniture industry can be classified into many segments based on materials used

Out of the above, Wood and wood based products (which include engineered wood panels such as Medium Density Fiberboards (MDF), plywood, particle boards- all processed from raw timber) garner a larger market share.
The wood panel industry is on the cusp of healthy expansion as the principal component for furniture manufacturing in India. As per Televisory report, the size of the wood panel industry in India is Rs. 28,000 Cr. and is estimated to grow at CAGR of 10% to 12%.
COMPONENTS OF WOOD PANEL INDUSTRY

These are also known as ‘engineered wood’, as they are processed from raw timber. As a cheaper, more durable, and eco-friendly alternative to wood, these products are gaining traction in the market. They are highly suitable to cater to the market demands of light weight, multipurpose furniture that confirms to the up-market style

- What is MDF?
Medium-density fiberboard (MDF) is an engineered wood panel that is formed by coalescing wood fibers obtained from breaking down hardwood and softwood in a defibrillator. It has a non-directional grain structure, making it an ideal wooden material for cutting, machining drilling processes without the production of chips or splinters. Furthermore, the absence of knot makes it easier for finishing, making it suitable for application in the interior decoration of houses and offices. MDF are usually denser than plywood, along with being considerably inexpensive. These factors make it an excellent alternative material for application wherein moisture resistant and very high impact resistance are not obligatory attributes. For instance, MDF is largely utilized in the assembly of furniture cabinetry and wood flooring subsurface.
- Raw Materials in MDF
MDF is typically made up of 82% wood fibre, 9% urea-formaldehyde resin glue, 8% water, and 1% paraffin wax
Rising trend in the cost of raw materials is a cause of worry for the MDF manufacturers. In the last 6 months, cost of chemicals/resins has increased by 70-80% due to sharp rise in Brent crude oil price which has gone up by 70% in last 6 months. Raw material prices are also impacted by higher container freight rates, strong dollar and price increase in origin countries.

Recent spurt in raw material prices and strong demand condition have encouraged the MDF manufacturers to go for price hike in the last few months. For example, Greenpanel hiked prices by 3% in South India and 6.5% in the rest of India between December 2020 and January 2021 due to an increase in raw material cost. Similarly, other manufacturers, including Century Ply, have hiked prices by 3-8% in last few months.
- Uses of MDF
- It is used in furniture such as in cabinets due to its strong surface,
- It is used as fire resistant material in building construction
- MDF boards are used as insulation and obstacle to vapors in many commercial as well as in residential buildings
- They are used for decorative purposes owing to its flexibility due to which it can be bend into any desired shape etc.

- Advantages of MDF - MDF has become a preferred choice for furniture manufacturers because:
- It gives very high-quality finishing
- It is suitable for precise machining techniques
- It is apt for manufacturing modern, branded, low-maintenance furniture
- It is suitable for the entire range of home furniture such as modular kitchen, wardrobes and others
- It is priced 50% cheaper than premium quality plywood and 25% to 30% cheaper than mid-range plywood

PARTICULARS | MDF | PLYWOOD |
Finish | Smooth and homogeneous in cross-section. | Smooth surface and a cross-section will show different layers or plies. |
Cost | Cheaper than plywood | More expensive |
Environmental impact | Eco-friendly, as it re-uses waste wood products | Less eco-friendly, as it uses wood veneers |
Workability | Can be shaped or moulded, and grooves can be cut. Using a router, smooth decorative edges can be created | Cannot be shaped or moulded, and grooves cannot be cut in the plywood. Cut edges are likely to be rough and have splinters |
Water resistance | Unless sealed on all sides and edges with primer, paint, laminate or membrane, etc, it will soak water and swell up | More resistant to water than MDF. However, all cut edges and surfaces should be well sealed |
Screw holding capacity | Lower screw holding capacity than plywood as the particles are very fine. If nailed at the edge of the board, it will split | Holds screws well. Can be nailed even at the edges |
Consistency of the board | Homogeneous, consists of fine particles | Consists of layers of wood veneer with the grains on each layer running in a different direction |
Strength | Less strong than plywood | The layers give additional strength |
Durability and Resilience | Durable when finished well. However, less durable than plywood | Durable when finished well. |
Maintenance | Should not be exposed to water. Need maintenance according to the surface finish: for example, laminates should be wiped clean, veneers can be polished | Should not be exposed to water. Needs maintenance according to the surface finish: for example, laminates should be wiped clean, veneers can be polished |
Weight-bearing capability | Sags under heavy weight as it is not stiff | Do not sag. Holds weight well if there are enough layers |
Flexibility | Inflexible board | Flexible in thin sheets |

COMPANY | YEAR OF COMMENCEMENT OF MDF PLANT | MCAP (in Rs. Crore) | CURRENT CAPACITY (in CBM p.a) | PROPOSED CAPEX (in CBM p.a) |
GREENPANEL | 2010 | 4,775 | 5,40,000 | 1,20,000 |
ACTION TESA | 2010 | UNLISTED | 4,20,000 | 2,00,000 |
RUSHIL DÉCOR | 2012 | 737 | 3,30,000 | - |
CENTURY | 2017 | 14,180 | 2,00,000 | 3,50,000 -3,60,000 |
GREENPLY | Mar, 2023E | 2,633 | - | 2,40,000 |
Due to sustained momentum in demand as well as prices, manufacturers are getting a clear revenue visibility, despite some price war in the market space. The capacity utilization in the industry has also gone up by 15% to 20% (i.e. 70-75% in 2021, which is expected to improve to 80-85% by 2025).
Industry experts believe that demand for MDF will match the increase in production capacity within the next couple of years.

There is a huge growth expected in the MDF industry for the abovementioned reasons. However, growth is only possible with the synchronized play of the underlying factors such as capacity expansion, efficient use of resources, quality improvements and growth in demand. Whether, any company would be able to capitalize such opportunities is dependent on how they outperform their peers.